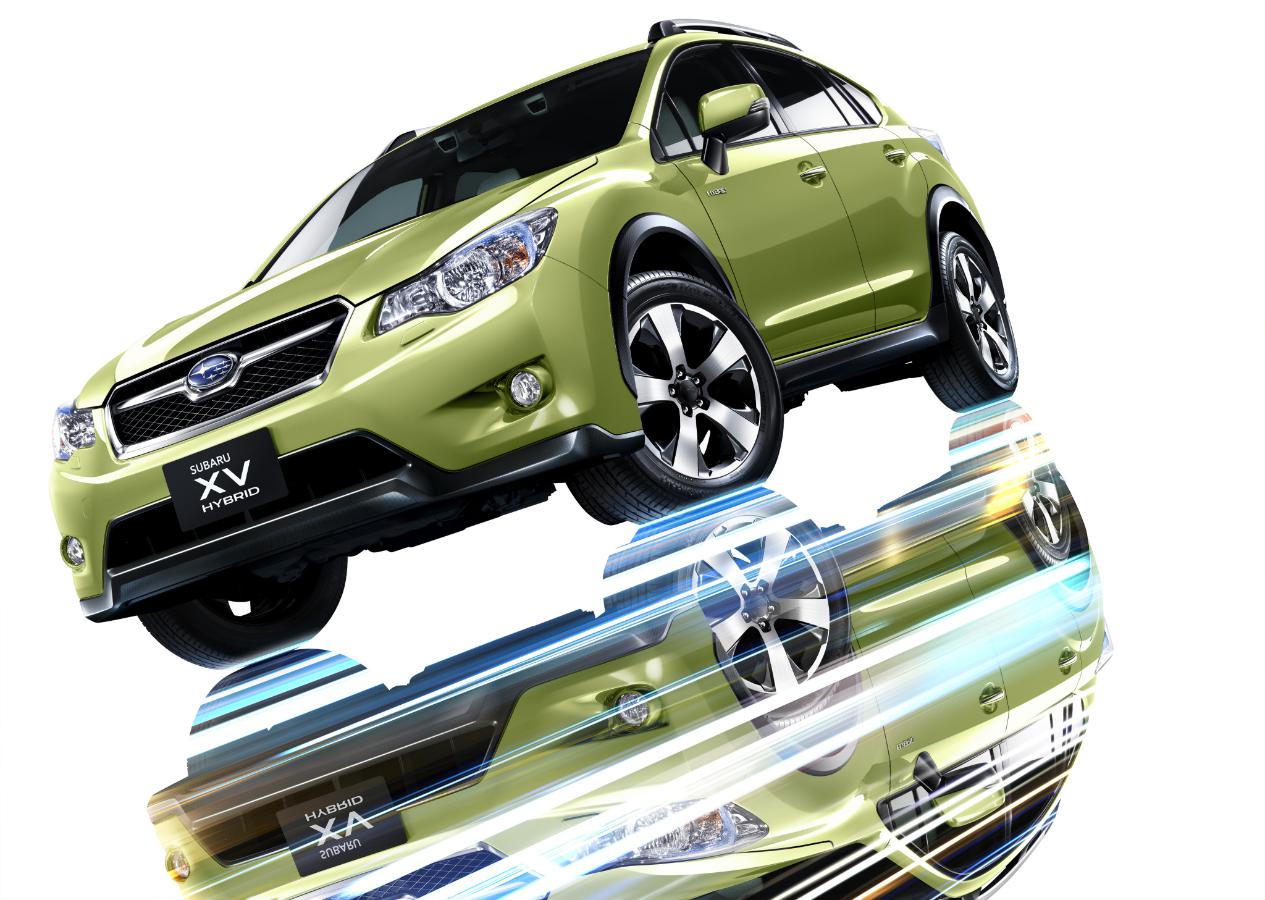
Voir la traduction automatique
Ceci est une traduction automatique. Pour voir le texte original en anglais cliquez ici
#IT & technologies - Telecom
{{{sourceTextContent.title}}}
Essai hybride de avancement de véhicule de Subaru par la simulation de Matériel-dans-le-Boucle
{{{sourceTextContent.subTitle}}}
? En adoptant la simulation FPGA-basée utilisant les plates-formes de matériel et de logiciel de Ni, nous avons réalisé la fidélité de vitesse et de modèle de simulation priée pour la vérification d'un moteur électrique ECU.
{{{sourceTextContent.description}}}
Nous avons ramené le temps d'essai à 1/20 du moment prévu pour l'essai équivalent sur un dynamomètre. ? ? M. Tomohiro Morita, FUJI Heavy Industries, Ltd.
Le défi :
Utilisant l'essai automatisé développer un nouveau système de vérification qui satisfait le niveau de qualité de commande a exigé pour le boîtier de commande électronique de moteur (ECU) dans Subaru ? véhicule hybride modèle de production de s premier, hybride de Subaru XV Crosstrek, et création des conditions d'essai laborieuses il est difficile réaliser qu'utilisant de vraies machines.
La solution :
Établissant un système de vérification avec la plate-forme de Ni FlexRIO qui rend l'exécution automatique de toutes les cartes-test possible et replie les environnements d'essai les plus graves pour assurer le de plus haut niveau de la sûreté à l'utilisateur, tout en obtenant le taux requis de commande et rencontrant des chronologies critiques.
Aujourd'hui, des automobiles sont équipées d'un énorme nombre d'ECU pour contrôler la fonctionnalité et les commandes avancées augmentées dans le véhicule. Dans un véhicule hybride, le moteur ECU joue un rôle bien plus compliqué pendant qu'il contrôle l'interaction entre le moteur conventionnel et le moteur électrique, avec ses systèmes d'alimentation.
Fuji Heavy Industries, maison mère mère de Subaru, présentée pour développer son premier véhicule hybride ? l'hybride de Subaru XV Crosstrek. C'était notre tentative préliminaire de livrer un véhicule hybride de modèle de production visant les marchés japonais et nord-américains domestiques.
Nos ingénieurs avaient développé un moteur ECU pour un premier prototype hybride, mais le composant n'a pas répondu aux exigences rigoureuses de prendre un véhicule au marché. Pour le véhicule de modèle de production, l'ECU a eu besoin de diverses fonctionnalités de commande pour empêcher des dommages au corps de véhicule et pour assurer la sûreté de conducteur et de passager dans de diverses conditions de fonctionnement, même les scénarios qui seraient ou impraticables pour examiner sur le matériel physique.
Par exemple, dans des conditions glaciales de conduite, une roue peut éprouver une perte soudaine de traction. Pendant l'accélération ceci peut causer une augmentation dramatique de de vitesse de moteur et les besoins d'être manipulé sans risque. Cependant, ce comportement de sûreté ne peut pas être physiquement reproduit sur un dynamomètre et est long et difficile à se reproduire sur une voie d'essai.
Puisque les algorithmes de commande complexes pour la sûreté spécifique conditionne comme ce besoin d'être développé et vérifié, l'essai a dû expliquer des conditions de fonctionnement périphériques pour satisfaire le niveau de qualité exigé pour un véhicule de modèle de production.
Une nouvelle approche
Nos ingénieurs ont relié l'ECU à une simulation en temps réel de moteur électrique pour examiner et vérifier une série de conditions, y compris les annexes extrêmes qui peuvent autrement casser le système dans l'essai mécanique traditionnel. Ils ont développé un mécanisme pour confirmer suffisamment cette approche de simulation de logiciel avec trois buts primaires pour l'essai réussi :
? Vérifiez la fonctionnalité d'ECU dans diverses conditions, y compris les environnements extrêmes pas facilement créés ou repliés
? Tracez les cas de test aux conditions d'assurer l'assurance complète d'essai
? Réalisez les essais de régression facilement pour valider rapidement des itérations de conception
Pour atteindre ces buts, notre équipe de technologie avait l'habitude une approche de V-diagramme pour lancer le processus de conception et de vérification. Le diagramme décrit une méthodologie échelonnée pour la conception de logiciel et la validation incluses de déploiement, y compris des points test de mesure à chaque étape.
Dans des étapes multiples du processus de conception, l'équipe a eu besoin du système de la matériel-dans-le-boucle (HIL) pour vérifier le moteur ECU contre une simulation en temps réel de moteur qui a exactement représenté le moteur réel de véhicule. En plus, utilisant le système de HIL, nos ingénieurs pourraient répondre à des exigences de traçabilité en enregistrant des résultats d'essai automatiquement et en automatisant des essais de régression quand une modification d'ECU a été apportée.
Succès de système
Le nouveau système de vérification établi se compose d'un vrai moteur ECU et du système de HIL qui simule des opérations de moteur. Le système de HIL peut représenter n'importe quelle condition de fonctionnement du moteur en plaçant des paramètres physiques tels que des inductances ou des résistances. Il peut également placer des paramètres de l'électronique de puissance, y compris des conditions de panne ou des scénarios d'essai tels que des combinaisons de charge serrez à la clé dynamométrique et avez désiré la vitesse tournante.
En changeant simplement un paramètre au milieu de l'essai, le système de HIL peut facilement simuler les scénarios complexes d'essai comme la perte précédente d'exemple de traction ou même un défaut de l'électronique de puissance dans l'inverseur qui détruirait le matériel physique. Quand l'opérateur demande une carte-test, le système de HIL répond la manière qu'un vrai moteur, et la réaction de système global peut alors être établie les renvois de avec des espérances pour valider que le contrôleur traite sans risque le cas de test.
Puisque l'exécution informatique exigée pour ce processus était si haute, nous nous sommes sentis que les instruments nationaux étaient le seul fournisseur qui pourrait répondre à ces exigences. Nous avons choisi le matériel de système de noyau basé sur les modules de Ni FlexRIO FPGA, qui sont les contrôleurs PXI-basés avec des morceaux de FPGA. Les modules ont exécuté un modèle représentant le fonctionnement simulé des moteurs, avec tous les programmes déployés utilisant le logiciel de conception de système de Ni LabVIEW.
Nous avons créé le scénario d'essai pour l'exécution séquentielle de chaque carte-test comme bilan d'Excel. Nous avons placé le moment pour l'étape d'exécution à 1 Mme et avons décrit les conditions d'essai, y compris le couple et la vitesse tournante, chronologiquement dans le bilan d'Excel. Selon ces conditions, le moteur ECU actionne et envoie des signaux, tels qu'un signal de modulation de largeur d'impulsion, au système de HIL.
Le système de HIL reçoit ces signaux puis simule le fonctionnement d'un vrai moteur. Plus spécifiquement, le processus informatique est effectué et le résultat est un résultat à la même vitesse que le vrai moteur. Les signaux en résultant représentant le couple et le courant triphase sont retournés au moteur ECU.
Pour chaque scénario d'essai, l'équipe a préparé des résultats d'essai de reportage de bilan d'Excel à l'avance, l'économie couple simulé et des valeurs courantes triphase aux étapes de 1 fois de Mme. Les valeurs obtenues à partir de l'essai de HIL ont été séquentiellement écrites dans le bilan d'Excel et comparées aux valeurs prévues correspondantes pour déterminer le résultat d'essai.
Nous avons automatisé le procédé de vérification utilisant LabVIEW pour lire et exécuter les bilans d'Excel pour les scénarios d'essai, avec des résultats obtenus écrits automatiquement au bilan d'Excel pour le rapport des essais. L'équipe a employé Visual Basic pour des applications dans Excel pour ce processus.
Avantages de choisir la plate-forme de Ni
Dans le système de HIL, le taux de boucle de simulation, équivalent de la résolution temporelle dans la simulation, était un facteur critique. Pour le moteur ECU, le taux de boucle a dû être 1.2 µs ou moins pour que le simulateur travaille. La plupart des plates-formes de simulation d'autres fournisseurs utilisent des unités centrales de traitement pour le calcul, ayant pour résultat un taux de boucle dans la gamme de 5 µs à 50 µs.
Ni FlexRIO a employé le FPGA pour que la commande et les buts informatiques répondent aux exigences de traitement, qui ont également fourni un avantage significatif en termes d'exécution de traitement informatique. La capacité d'atteindre le taux exigé de simulation à 1.2 µs était le facteur décisif pour adopter la plate-forme de Ni FlexRIO pour ce système.
En plus, parce que le Ni FlexRIO a une mémoire à accès sélectif dynamique de grande capacité et intégrée, pourrions-nous employer le modèle de JMAG-RT fourni par JSOL Corp. ? chaîne d'outil logiciel de s JMAG. Ceci a permis pour représenter les caractéristiques fortement non linéaires plus près du vrai moteur.
D'ailleurs, nos ingénieurs pourraient programmer le FPGA sur le dispositif de Ni FlexRIO graphiquement avec le module de Ni LabVIEW FPGA, qui a permis pour développer un système avec l'armature de technologie de FPGA en peu de temps sans employer une langue basée par texte telle qu'un langage de description de matériel.
Toutes les cartes-test développées peuvent être courues automatiquement en seulement 118 heures. La réalisation de tous les essais manuellement prendrait des 2.300 heures environ. L'essai automatisé atténue également le risque et le temps additionnel liés aux erreurs humaines qui peuvent se produire avec l'essai manuel.
Le système de HIL a fourni les avantages éonomiseurs de temps additionnels qui ont inclus une réduction significative du nombre de procédures d'installation, telles que préparer un banc de moteur et un véhicule d'essai, et il a enlevé le besoin du personnel d'essai d'être qualifié pour manipuler l'équipement à haute tension.
